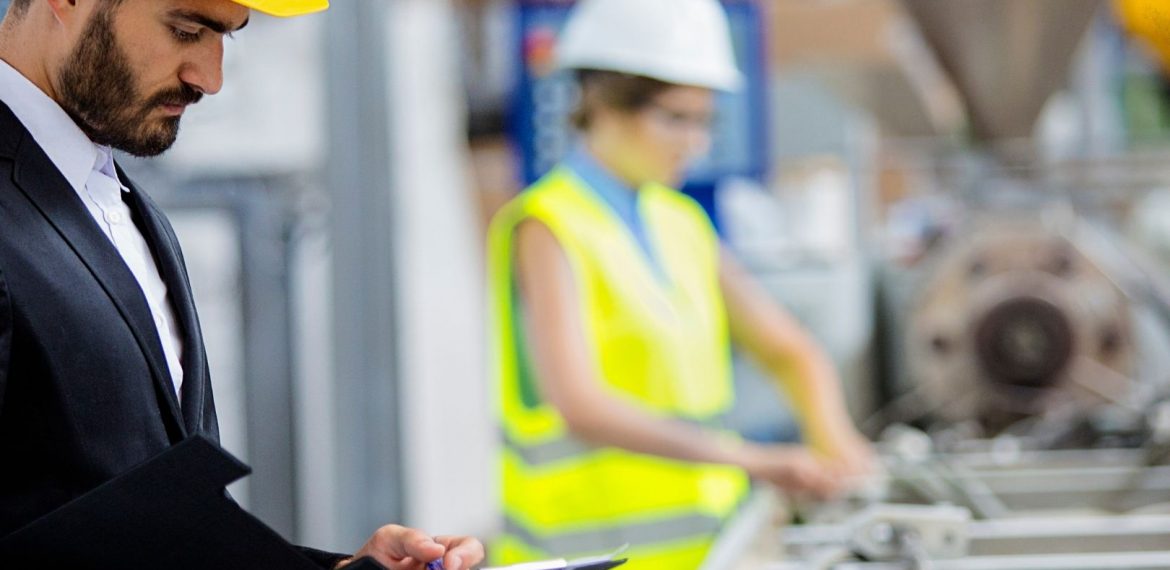
Lean Production and Production Planning in the LPOne development vision #postblog4
Lean Production and Production Planning in the LPOne development vision #postblog4
Strong integration between management database and physical line devices
In this fourth and last post dedicated to Lean Production and Production Scheduling in the LPOne development vision, we will address the first assumption that must lead to the definition of concrete management objects that an ERP software should have in order to provide adequate support to modern production scheduling. Then we will talk about: High integration between the management database and the physical online devices.
After set-up, a line must be able to enter the operational phase with adequate control over operations and effective management of the following processes:
- re-stocking of line warehouses,
- streamlined rework management,
- dynamic tack time detection,
- product and material traceability,
- suspension/restoration of operations.
LPOne implementation
The lean production management system based on LPOne includes a set of external physical devices that form a true IoT ecosystem. Smart devices such as scales, traffic lights, barcode readers, printers and touch screens are interconnected as shown in the figure below:
The “Production Line Orchestrator” engine implements the line workflow mentioned in the previous paragraph, while the “IoT Interfacing System” collects and sends signals to the production line to implement the workflow.
An important part is the re-stocking of the line warehouse, which is managed by means of an electronic Kanban and weight-based underwriting with integration to the mobile warehouse devices. This makes it possible to implement a pull replenishment logic directly on the devices in the hands of the warehouse operators, who can concentrate on routine movements in peace and quiet and be notified in good time when a replenishment is required, thus avoiding downtime problems.
Reworks are also handled dynamically, allowing a sub-assembly to leave the production process to be checked and repaired if necessary, and then re-enter the production process where it left off, without the need for downtime.
The barcode readers between the various stations allow both the sending of commands and requests (e.g. quality control requests) and the tracing of the passage of each sub-assembly from one station to the next, so as to continuously monitor the progress of the production process and continuously detect the tackt time.
This continuous and real time detection, allows both to verify the balance of the stations and to use a predictive algorithm based on neural networks, able to learn and correlate the variations of takt time and the occurrence of defects, in order to act with preventive control requests.
Conclusions
The name of our product, LPOne, stands for Lean Production One. If the Latin phrase nomen omen is true, InnoTech can only support its vocation for innovation through technology by enriching its flagship product for advanced production management with specific functionality for Lean Production. This commitment follows the experience gained from the implementation of countless successful projects in the field of production management based on SAP Business One and LPOne.
Our guiding principles have been, as more fully described in this article, the following:
- Introduction of a point of discontinuity between commercial and production programming.
- Implementation of fast support for line configuration.
- Use of IoT and AI technology to integrate the ERP with physical line devices.
The development of the three previous points, derived from our experience and in-depth knowledge of lean paradigms, has enabled us to create an advanced hardware and software system applicable in real discrete production environments.
We therefore believe that we have achieved not only innovation, but also improvement and evolution of process management in the increasingly complex and fast-paced world of production activities, enabling the ERP system to provide concrete support for production management with a view to efficiency, effectiveness and user satisfaction.